La substitution des plastiques par des matériaux fibreux
TECHDAY #2
As the automotive industry shifts toward greener alternatives, the challenge of replacing plastics with natural and recycled fibrous materials has never been more crucial.
We are delighted to invite you to our upcoming
TechDay #2
on the theme « Car Parts: Replacing Plastics with Fibrous Materials, »
which will take place on November 21, 2024, at ENSAIT, Roubaix, from 09:00 to 16:30 (with registration from 08:30).
This event will bring together manufacturers, technical centers, R&D experts, research laboratories, and anyone with an interest in exploring innovative approaches to sustainable materials in the automotive sector.
Our focus will be on natural fibers, recycled fibers, natural composites, eco-design, sustainability, end-of-life solutions, circular economy for automotive industry.
Event Highlights
- Presentations (15 minute-pitch/5 minute Q&A session):
expert-led presentations with insights on cutting-edge research, technological advances, and practical industrial applications
- Networking lunch with demonstrators:
participants are invited to bring demonstrators or prototypes to showcase during the networking lunch, offering an opportunity to exchange ideas and foster collaborations (subject to availability; register your interest using the registration form)
Secure your spot at the TechDay and drive the change toward a greener future!
Agenda :
08:30 – Registration / Welcome coffee
09:00 – Welcoming words
By the Organizers & Jean-Marc VIENOT, Vice President, ENSAIT
09:10 – Clémence LIEBERT, Circular Economy Manager, PFA
« Context for the integration of sustainable materials in the automotive sector: regulatory constraints and environmental objectives for a sustainable transition. »
This presentation will explore the challenges of decarbonisation and the circular economy in the automotive industry and the opportunities for using sustainable materials to meet these challenges.
09:30 – Simon FREMEAUX, Fibres and nonwovens expert, CETI Transformative textiles
« Natural and recycled fibers in automotive: challenges and opportunities »
Natural and recycled fibers present significant potential for the automotive sector, offering environmental benefits, weight reduction, and enhanced cabin aesthetics. However, they face challenges such as variability in quality, lower durability under extreme conditions, and compatibility with manufacturing processes. Despite these hurdles, advancements in processing technologies and growing demand for eco-friendly materials drive their adoption. This shift could pave the way toward a more sustainable automotive industry, blending performance with reduced environmental impact.
09:50 – Stéphane COUTEAUD, Development & Technical sales engineer, EcoTechnilin
« Natural fibers in the automotive industry, what is, what could be »
In today automotive industry some reinforcement parts are already made with natural fiber non-woven mat. The manufacturing process creates co-products that today are treated as waste.
The case study of the Recytal process by EcoTechnilin, will present a manufacturer agility and ability to propose a new business model : build a circular and virtuous economy circle with its advantages in CO2 emission and better cost benefit. The case will also highlight the barrier innovation can face in the automotive industry.
The prospective will be on the next step – visible natural fibers in vehicles »
10:10 – Cécile MARTIN, Innovation and recycling manager, Refashion
« From textile waste to technical nonwovens for the automotive industry »
Car manufacturers have made some undertakings to use more recycled materials in newly designed vehicles. The expected features of products manufactured with these materials are: acoustic performance, lightness, and recycled and recyclable content. Refashion launched a collaborative Working Group in 2020 to develop a high-performance insulating nonwoven made from post-consumer clothing collected in France. The Working Group enabled to create a technical nonwoven meeting the requirements of automotive suppliers. The industrial value chain still has to be validated, with the ongoing automatisation of post-consumer textile materials sorting and preprocessing to optimize production costs.
10:30 – Networking & exhibition
10:50 – Christophe TIRLEMONT, Product & Process Innovation Manager, Eurostyle Systems
« Decorative natural fibers for automotive interior parts »
NFPP (Natural fiber (NF) and polypropylene (PP) composites) : material, processing, validations done for automotive interior parts through a prototype tool (press forming with back injection). Benefits in term of weight and CO2 reduction
11:10 – Mélissa POLONI, Research engineer, CEA-Liten
« Properties of PLA / natural fibers composites »
As part of a European project, the CEA experimented with the idea of replacing polymers of fossil origin (PMMA and ABS-GF) used via 2K injection in car side pillars, with biobased composites such as PLA filled with flax or hemp fibers. The automotive world has specific requirements such as the aesthetic appearance of parts, their thermal resistance and their mechanical performance, and this talk will address the properties obtained during this project for such composites.
11:30 – Delphine NOTTA-CUVIER, Assistant Professor, LAMIH UMR CNRS 8201
« Impact of natural variability of vegetal fibres’ properties on mechanical properties of injection-moulded composite parts »
Today, numerous automotive parts are made of short-fibre reinforced thermoplastics, processed by injection moulding. By far, short-glass fibre reinforced polypropylene (PPGF) is the most used composite but replacing glass fibres by vegetal fibres is an appealing solution to save weight and increase the proportion of biosourced materials in automotive parts, among other advantages. However, vegetal fibres are characterised by a complex structure and a possibly huge variability of geometrical and mechanical properties. Lack of knowledge about real impact of variability at the fibre scale on mechanical behaviour at specimen or part scale is still a major obstacle for a more widespread use of short-vegetal-fibre reinforced thermoplastics.
11:50 – Alain CHOQUET, Senior Marketing Manager, Motherson
« Miscanthus fibers to reinforce automotive molded components »
In purpose to reduce plastic injection carbon footprint, according with the future weather conditions Motherson has developed a polypropylene resin reinforced with miscanthus fibers able suitable to make instrument panels substrates, in partnership with one compounder and one OEM
12:10 – Lunch break ; Networking & exhibition
13:15 – Frederik GOETHALS, Research scientist, CENTEXBEL
« Biobased resin formulations and sustainable reinforcements to make lightweight composite parts for the automotive sector »
This presentation will showcase results of the Horizon Europe project Suspens, with a focus on the development of innovative biobased resin formulations and sustainable textile reinforcements. These materials can be used to produce composite parts for the automotive industry, offering a sustainable alternative to traditional fossil-based composites. By utilizing recycled and bio-sourced materials, the project aims to reduce the environmental footprint of automotive composite parts while maintaining the performance and durability of conventional materials
13:35 – Marc COMI BONACHI, Research And Development Specialist, VITO
« Lignin as Sustainable Alternative to Gradually Replace Traditional Bisphenols in the Thermoset Industry »
As a leader institution in sustainability, VITO aims to replace fossil-based bisphenols in epoxy resins with biobased alternatives, primarily targeting the environmental and health impacts of bisphenol A (BPA), especially in composites and coating applications. BPA is widely used in epoxy resins but poses risks due to its endocrine-disrupting properties. In last years VITO enhanced the expertise in producing alternative biobased building blocks to BPA, as well as, recycling BPA from end-of-life plastics, to develop dual-renewable epoxy formulations that ensure high performance. VITO is focusing on producing biobased resins using lignin, which is treated, depolymerized, and modified to create lignin-based resins. Scale up lab production while ensuring sustainability through rigorous testing and a Safe and Sustainable by Design (SSbD) approach is deeply considered. Biobased resins prototypes are tested on various performance conditions, demonstrating strong adhesion and a protective barrier against external agents such as radiation, moisture, and chemicals.
13:55 – Jean-Luc LANFRANCHINI, Group VP R&D, Trèves
« Fibrous materials in automotive applications as a substitute to plastics »
The European « »Fit for 55″ » package has emphasized the need for a disruption in the car industry. Weight saving together with circular economy become key to reduce drastically CO2 emissions all along the product life cycle. As a leader of soft trims and acoustics, Treves Group has developed innovative solutions to support the OEMs in their weight reduction targets and their willingness to introduce recycled materials from End Of Life vehicles and post consumer/industrial wastes.
Through the example of underbody parts, we will show how we’ve been able to offer a complete range of fibrous solutions to match with the OEMs specs while improving the acoustics of the vehicle.
14:15 – Yves FOSTIER, Christophe STAMFELJ & Iqra AZIZ, Région Hauts-de-France
« Driving Interregional Innovation: Funding Opportunities for Sustainable Mobility »
Presentation of ongoing funding opportunies that can fuel your organization’s growth in the green transition ! This session explores strategic calls for projects that support sustainable mobility, circular economy practices, and cross-border partnerships.
14:35 – Networking & exhibition
14:55 – Philippe Vroman, Associate Professor – Innovative & Bio-inspired Nonwoven Materials ENSAIT – GEMTEX Laboratory
« Opportunity of developing circular composites from recycled PP-based/textile materials for car industry and interior design »
The COVID-19 health crisis highlighted the problem of the end-of-life of respiratory protection masks (surgical masks, FFP2) and other disposable PPE (gowns, surgical drapes, overshoes, etc.). Our project offers an innovative, cost-effective solution for developing composite materials made from these recycled materials. Target applications include automotive reinforcement parts mixed with flax fibres and interior design objects mixed with recycled textiles. Results in terms of mechanical behaviour will be presented, as well as creations made in collaboration with designers.
15:15 – Philippe DESRAMAUX, WTX Automotive Group
« From plastics to nonwoven:a material shift in the automotive industry »
The automotive industry has long relied on plastic resins, with key milestones marking the evolving use of plastics to meet demands for lightweight, durable, high-performing vehicles. Now, a new material is gaining momentum: nonwoven fabrics. Introduced at pivotal moments in automotive manufacturing, nonwovens are rapidly growing in popularity. Why the rise? Nonwoven materials offer substantial benefits in terms of weight reduction, acoustic performance, and overall efficiency, making them a perfect complement to plastics. While they won’t entirely replace plastics, they represent a natural evolution with exciting new applications. Additionally, the surge in electric and hybrid vehicles is driving up demand for nonwoven materials, prized for their ability to improve thermal and acoustic insulation while reducing vehicle weight.
16:00 – Wrap up & conclusions of the day
Secure your spot at the TechDay and drive the change toward a greener future!
Date & Time: November 21, 2024, from 09:00 to 16:30 (Welcome from 08:30)
Venue: ENSAIT, Roubaix, 59
Language: English Fees : Rate for members (ARIA Hauts-de-France, EuraMaterials, Agoria, RAI Automotive, GPA) : 120€ TTC (ask for your promotional code : Amandine CAUX) Rate for non-members : 180€ TTC Speakers’ companies: 3 free tickets (ask for your promotional code : Amandine CAUX)
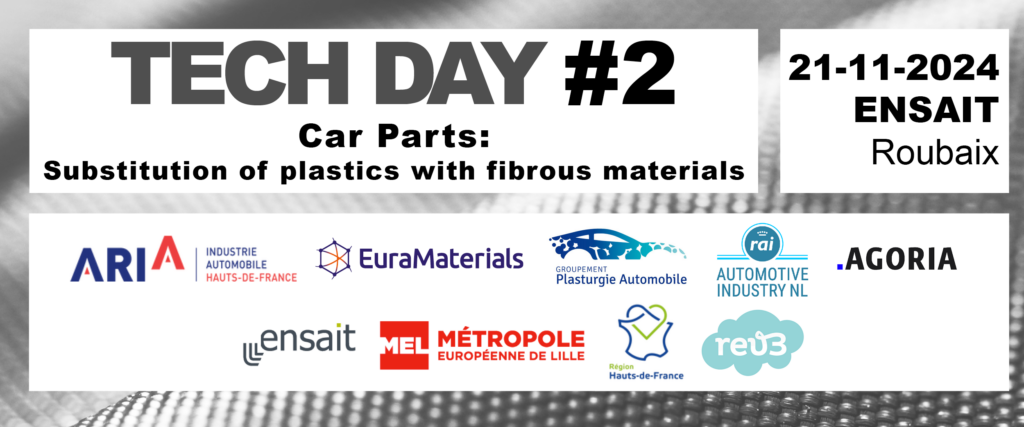